Understanding the Key Elements and Repair Techniques for Packaging Equipment Maintenance
Reliable maintenance of packaging makers pivots on a comprehensive understanding of their vital components, consisting of the frame, drive system, and securing devices. Acknowledging usual upkeep problems, coupled with the implementation of preventative techniques and repairing methods, can dramatically improve equipment reliability.
Secret Elements of Packaging Makers
Packaging devices are composed of several essential elements that collaborate to ensure reliable and efficient product packaging processes. At the core of these devices is the framework, which gives architectural stability and houses the various operating parts. The drive system, often a mix of motors and gears, assists in the activity of parts, enabling accurate operation throughout the packaging cycle.
Another important component is the conveyor system, which transports items through different phases of the product packaging process. This is typically complemented by sensors and controls that keep track of the position and speed of products, making sure synchronization and lessening mistakes. The loading system is essential for properly giving the appropriate amount of item right into plans, whether in fluid, powder, or strong type.
Sealing systems, including heat sealers or glue applicators, play a vital function in protecting packages, avoiding contamination and prolonging service life. Additionally, classifying systems are indispensable for giving essential item info, guaranteeing compliance with policies. Lastly, the control board, outfitted with straightforward user interfaces, allows drivers to take care of maker features, display performance, and make adjustments as required, making certain ideal efficiency and efficiency in product packaging procedures.
Typical Maintenance Issues
Reliable operation of packaging makers relies greatly on routine upkeep to avoid common issues that can disrupt manufacturing. Amongst these problems, mechanical deterioration is common, specifically in components like electric motors, conveyors, and seals, which can cause unexpected downtimes. Additionally, misalignment of parts can result in ineffective procedure, creating products to be inaccurately packaged or damaged during the procedure.
Another typical upkeep issue includes the buildup of dust and particles, which can interfere with the equipment's sensing units and relocating parts. packaging machine repair service. This not just affects efficiency yet can also present safety and security dangers. Lubrication failings can lead to boosted friction, resulting in getting too hot and eventual element failure.
Electric troubles, usually coming from loosened connections or worn-out electrical wiring, can disrupt equipment functions, leading to considerable production delays. Software application glitches due to incorrect configurations or out-of-date programs can prevent the equipment's procedure, requiring instant intervention. Dealing with these common maintenance issues proactively is vital for making certain optimal performance and long life of product packaging machinery.
Preventative Upkeep Methods
Applying preventative upkeep methods is essential for sustaining the effectiveness and dependability of product packaging makers. These strategies incorporate a systematic technique to maintenance, concentrating on the normal assessment and maintenance of devices to preempt possible failures. By sticking to a scheduled upkeep program, operators can recognize damage on elements before they bring about considerable breakdowns.
Trick aspects of a preventative maintenance approach consist of routine inspections, lubrication, part, and cleansing substitutes based on producer recommendations. Using checklists can simplify this procedure, making certain that no essential tasks are overlooked. Additionally, keeping accurate documents of maintenance tasks help in tracking the device's performance with time, assisting in notified decision-making regarding future upkeep requirements.
Training personnel on the importance of preventative upkeep improves conformity and fosters a society of positive care. Applying an anticipating upkeep element, utilizing data analytics and sensing unit innovation, can better maximize equipment performance by anticipating failures prior to they take place.
Fixing Methods
When confronted with breakdowns or ineffectiveness in packaging makers, employing methodical troubleshooting strategies is important for identifying here are the findings and solving issues swiftly. The initial step in efficient troubleshooting is to establish a clear understanding of the maker's operational criteria and performance metrics. This entails examining the maker's requirements, as well as any kind of mistake codes or notifies shown.
Following, drivers need to conduct a visual evaluation, looking for noticeable signs of damage, wear, or imbalance. This typically includes analyzing gears, belts, and sensors to determine possible you can find out more root causes of malfunction. Gathering functional information, such as production rates and downtime logs, can likewise supply understandings right into repeating issues.
As soon as prospective issues are determined, utilizing a rational method to separate the source is critical. This may need testing specific elements or systems in a regulated way. Taking part in conversations with operators that interact with the equipment routinely can generate valuable comments concerning unusual habits or patterns.
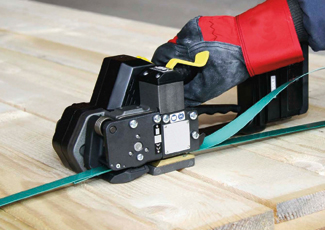
Repair Work and Substitute Best Practices
An extensive understanding of repair and replacement ideal methods is crucial for keeping the longevity and effectiveness of product packaging machines. Regularly examining the problem of machine elements allows for prompt intervention, stopping even more substantial issues that go to these guys can bring about costly downtimes.
When fixings are required, it is vital to use OEM (Original Tools Manufacturer) parts to guarantee compatibility and performance. This not just maintains the honesty of the device however also supports guarantee arrangements. Furthermore, it is a good idea to keep an inventory of critical spare parts to facilitate quick replacements and reduce functional disturbances.
For intricate repairs, involving certified technicians with specialized training in product packaging equipment is recommended. They possess the competence to identify problems properly and execute repair work successfully. Additionally, recording all fixing tasks and parts substitutes is crucial for keeping a detailed upkeep history, which can aid in future troubleshooting.
Last but not least, applying a positive method, consisting of normal examinations and predictive maintenance methods, boosts the dependability of product packaging devices. By sticking to these best techniques, organizations can ensure ideal machine efficiency, decrease functional dangers, and expand devices lifespan.

Conclusion
In final thought, a complete understanding of product packaging equipment components and effective maintenance methods is essential for optimal efficiency. By carrying out these practices, organizations can guarantee the longevity and effectiveness of product packaging devices, ultimately contributing to improved operational efficiency and minimized expenses (packaging machine repair service).
Efficient upkeep of product packaging machines hinges on a complete understanding of their vital elements, consisting of the structure, drive system, and securing devices.Efficient operation of packaging devices depends heavily on routine maintenance to avoid typical issues that can interfere with manufacturing.Carrying out preventative maintenance techniques is vital for maintaining the performance and integrity of product packaging devices. Additionally, keeping accurate documents of maintenance activities help in tracking the device's performance over time, promoting educated decision-making concerning future maintenance demands.
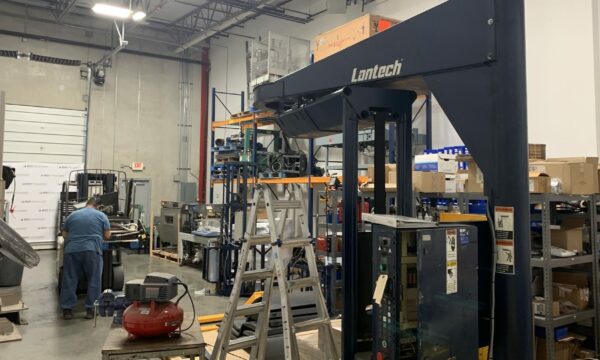
Comments on “Relied On Packaging Machine Repair Service for Long-Lasting Devices Efficiency”